Welded joints are a widely used method of joining materials in various industries and applications, ranging from construction to manufacturing, automotive, and aerospace.
The process of welding involves melting and fusing two or more materials, creating a permanent bond that is often stronger than other joining methods, such as bolting or riveting.
Welding can be used to join a wide range of materials, including metals, plastics, and composites, making it a versatile option for many different applications.
However, while welded joints offer several advantages, such as high strength, versatility, and cost-effectiveness, they also have some disadvantages, such as the need for skilled labor, potential for distortion, and safety concerns.
In this article, we will delve deeper into the pros and cons of welded joints and explore when to use them.
Welded joints- pros and cons
Pros | Cons |
---|---|
High Strength | Skill-Dependent |
Versatility | Time-Consuming |
Cost-Effective | Potential for Distortion |
Clean Appearance | Safety Concerns |
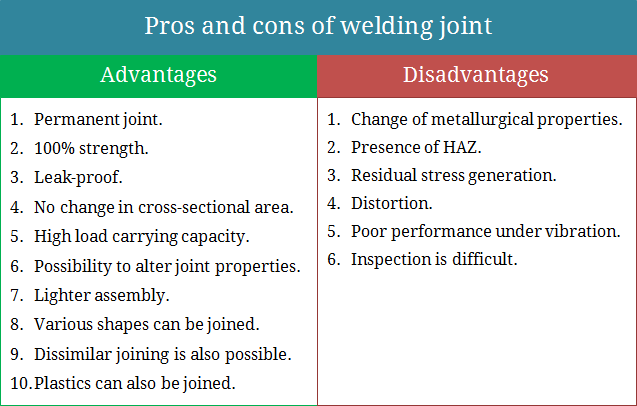
Advantages of Welded Joints:
- High Strength: Welded joints are known for their high strength and durability. A properly executed welded joint can provide a stronger bond than other types of joints, such as bolted or riveted joints. This is because welding melts the materials together, creating a metallurgical bond that is stronger than a mechanical connection.
- Versatility: Welded joints can be used to join a wide variety of materials, including metals, plastics, and composites. This makes them a versatile option for many different applications, from automotive manufacturing to construction.
- Cost–Effective: Welding is a relatively low-cost method of joining materials, particularly for high-volume production. It requires minimal tooling and can be automated to increase efficiency and reduce labor costs.
- Clean Appearance: Welded joints can create a clean and aesthetically pleasing appearance, particularly for applications where the joint will be visible, such as architectural metalwork.
Disadvantages of Welded Joints:
- Skill–Dependent: Welding is a skilled trade, and the quality of the weld depends heavily on the expertise of the welder. A poorly executed weld can result in a weak joint that may fail under stress.
- Time–Consuming: Welding can be a time-consuming process, particularly for complex joints or large structures. This can result in longer production times and higher costs.
- Potential for Distortion: Welding can cause distortion in the materials being joined, particularly in thinner materials or when welding dissimilar metals. This can affect the fit and function of the finished product.
- Safety Concerns: Welding can pose safety hazards, including exposure to hazardous fumes, intense heat, and electrical hazards. Proper training and safety equipment are essential to prevent injury or illness.
When to use welded joints?
Welded joints are commonly used in many different industries and applications. Here are some scenarios where welded joints are often used:
Structural Applications: Welded joints are often used in structural applications, such as in the construction of buildings, bridges, and other large structures. Welding provides a strong and durable bond between materials, which is essential for ensuring the stability and safety of these structures.
Manufacturing: Welded joints are widely used in the manufacturing industry, particularly for the production of metal products. Welding can be an efficient and cost-effective method of joining materials in high-volume production environments.
Automotive Industry: Welded joints are commonly used in the automotive industry for joining metal components. This includes both structural components, such as the frame and body of a vehicle, as well as smaller components, such as exhaust systems.
Aerospace Industry: Welded joints are also used extensively in the aerospace industry for joining metal components. Welded joints provide a strong and reliable bond that can withstand the stresses and strains of flight.
Repair and Maintenance: Welding is often used for repair and maintenance tasks, such as repairing damaged metal components or welding new sections onto existing structures.
In general, welded joints are a good choice when a strong, durable, and permanent bond is required between materials. Welding can be used to join a wide variety of materials, including metals, plastics, and composites, making it a versatile option for many different applications. However, it is important to consider the potential disadvantages of welded joints, such as the need for skilled labor and the potential for distortion, when deciding whether to use welding as a joining method.
Types of weld joints:
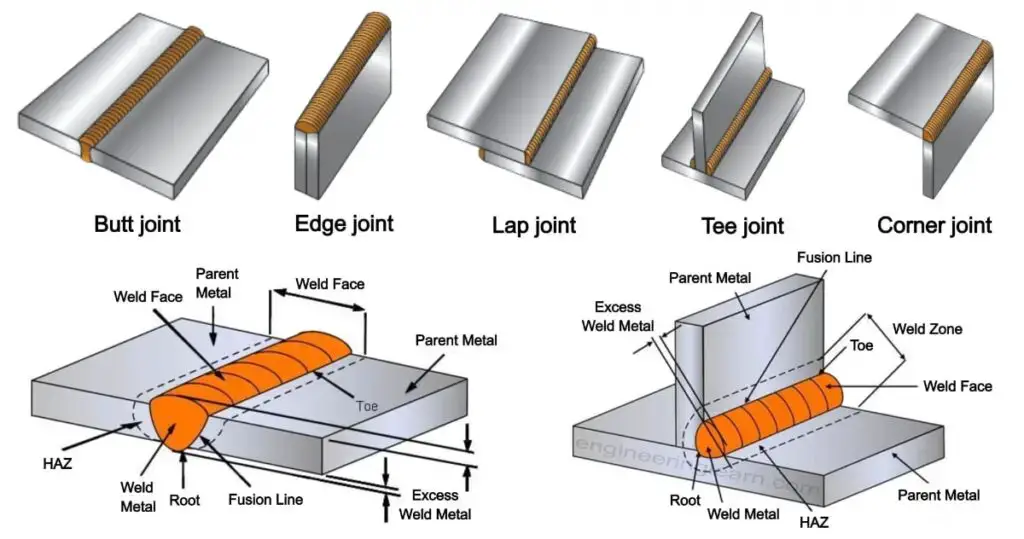